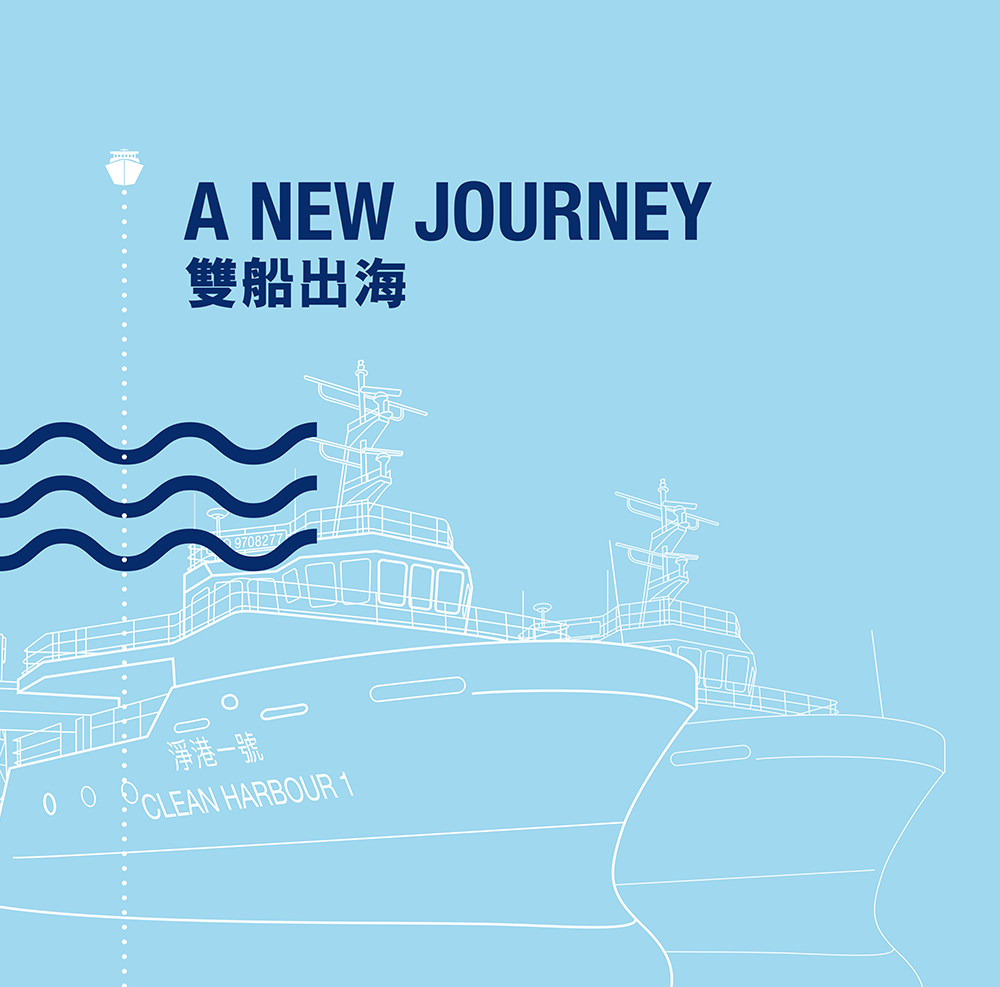
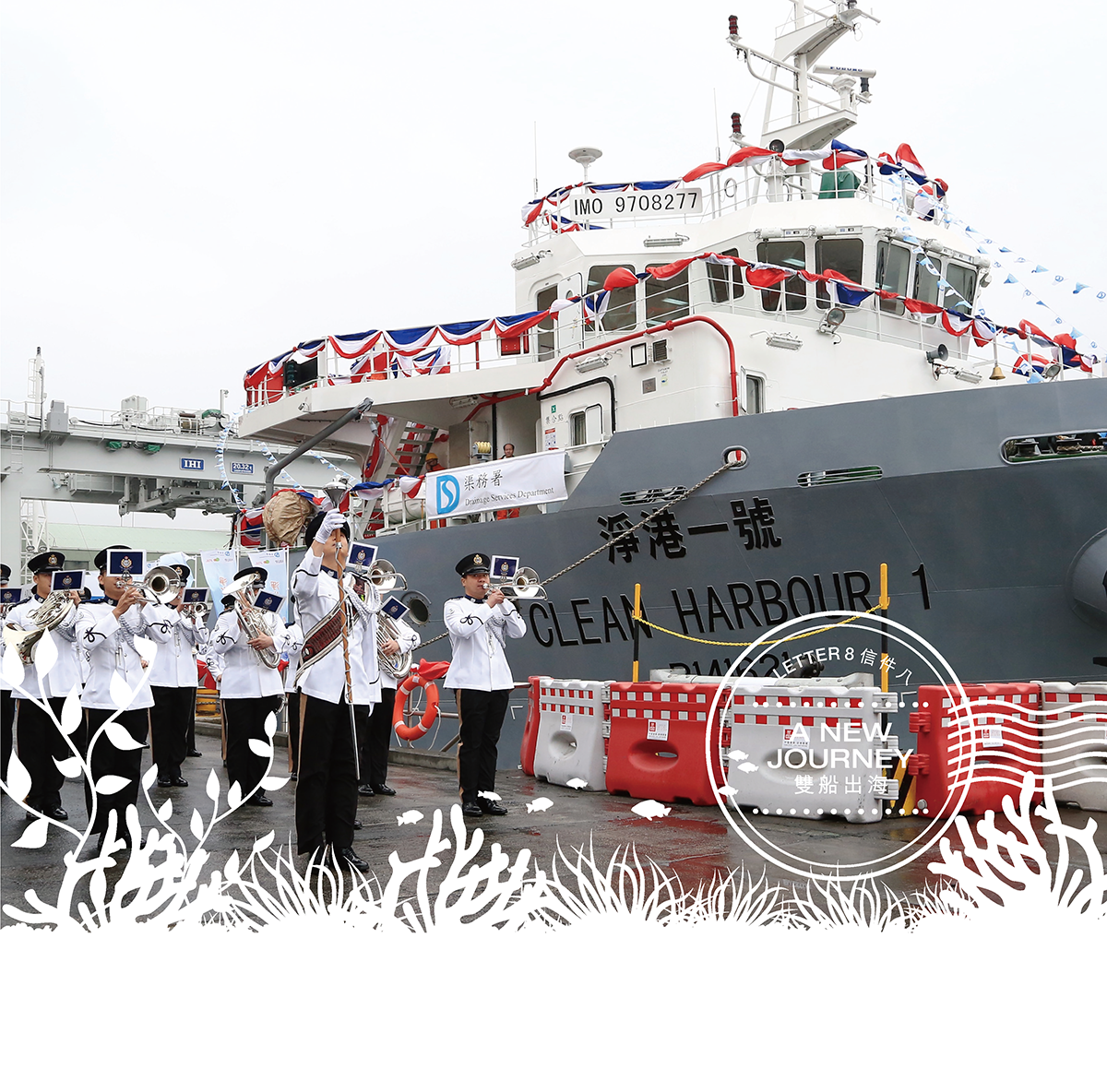
Dear Harbour,
One of the delights of working on the HATS project was that it took us on unexpected adventures, such as the building and commissioning of two ocean-going vessels!
This is the story of how the project team built Clean Harbour 1 and Clean Harbour 2 — advanced vessels tailor-made for the transportation of sludge from Stonecutters Island Sewage Treatment Works (SCISTW) to T · PARK at Tuen Mun for incineration to generate electricity, thereby completing the waste-to-energy sustainability loop.
Sludge and T · PARK: Waste to Energy
When HATS Stage 1 was commissioned in December 2001, landfilling was the only means of sludge disposal in Hong Kong. Sludge was therefore transported on container trucks to the South East New Territories Landfill and the West New Territories Landfill for disposal. However, the amount of sludge increased rapidly from around 600 tonnes daily in the early 2010s to 800 tonnes daily by late 2015 after the commissioning of Stage 2A, and is expected to eventually rise to around 1,200 tonnes daily. The Government soon found that this was not a sustainable waste management solution. The large amount of sludge from HATS Stages 1 and 2A was shortening the lifespan of the landfills.
In contrast, incineration is a much better way to dispose of sludge. Burning sludge at ultra-high temperature of above 850 degrees Celsius, converts it into ash and residue, reducing the original sludge volume by as much as 90%, and dramatically cuts the quantity of waste to be disposed of at the landfills.
After much deliberation, the Government decided to create T · PARK as Hong Kong’s first self-sustaining sludge treatment facility. At T · PARK, sludge is incinerated to generate heat energy that is harvested and turned into electricity to support the power requirements of various park facilities, including a day spa and a range of recreational and environmental education facilities for the public. Surplus electricity is fed into the power grid, forming an impeccable waste-to-energy cycle.
T · PARK can handle up to 2,000 tonnes of sludge per day, more than adequate to incinerate the sludge from SCISTW and other sewage treatment works. In March 2015, HATS began transporting dewatered sludge from SCISTW to T · PARK for incineration, using two purpose-built ocean-going vessels.
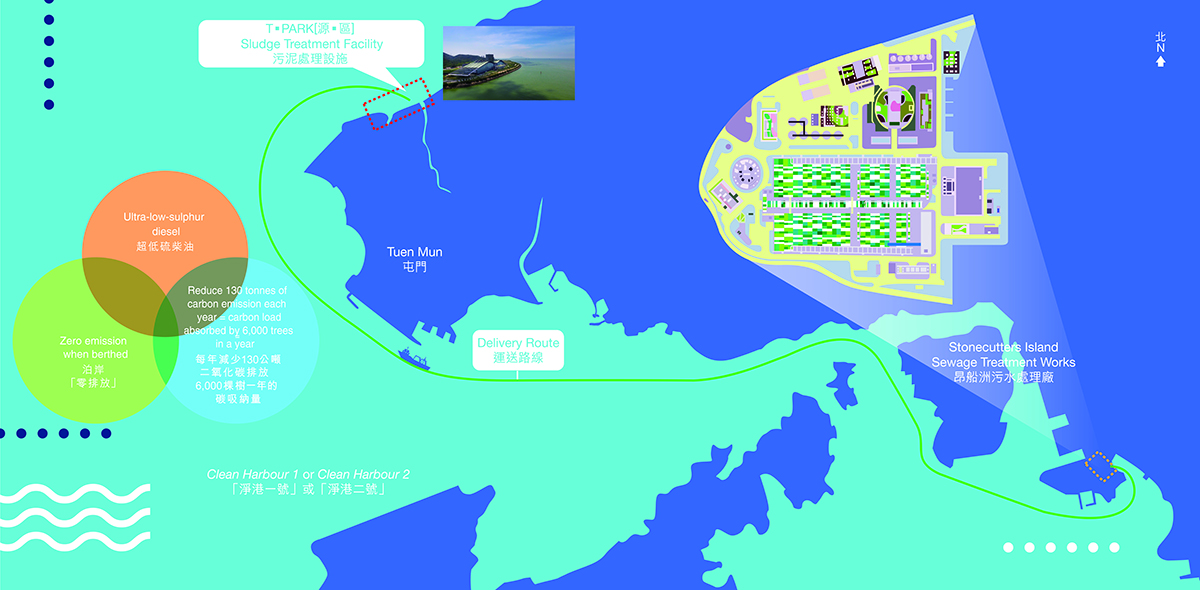
Clean Harbour 1 and Clean Harbour 2
To bring the sludge to T · PARK, sea transportation was preferred as it would eliminate environmental nuisance and traffic impact compared to land transport using container trucks. If container trucks were to be used for transferring sludge to T · PARK, around 60 truck trips would be expected every day since late 2015, and so impacting on the traffic conditions of the trunk roads from SCISTW to T · PARK. The project team thus began talking to overseas vessel building experts to identify the best design with environmental features.
A Design-Build-Operate contract was eventually let for the building of two ocean-going vessels and their operation for 10 years, with a five-year extension. This arrangement was chosen to incentivise the contractor to adopt state-of the-art technologies. The vessels were named Clean Harbour 1 and Clean Harbour 2.
Each vessel can handle up to 90 sludge containers per trip, corresponding to about 1,200 tonnes of sludge. Transporting sludge in ocean-going vessel is superior to conventional barge transportation, as a typical barge can only carry about 50 containers of sludge and its operation must be suspended whenever typhoon signal No.3 or above is hoisted. Ocean-going vessels, on the other hand, may continue operating up to typhoon signal No. 8, helping avoid a backlog in the Sludge Dewatering Facility and sludge cake silos on SCISTW during adverse weather conditions.
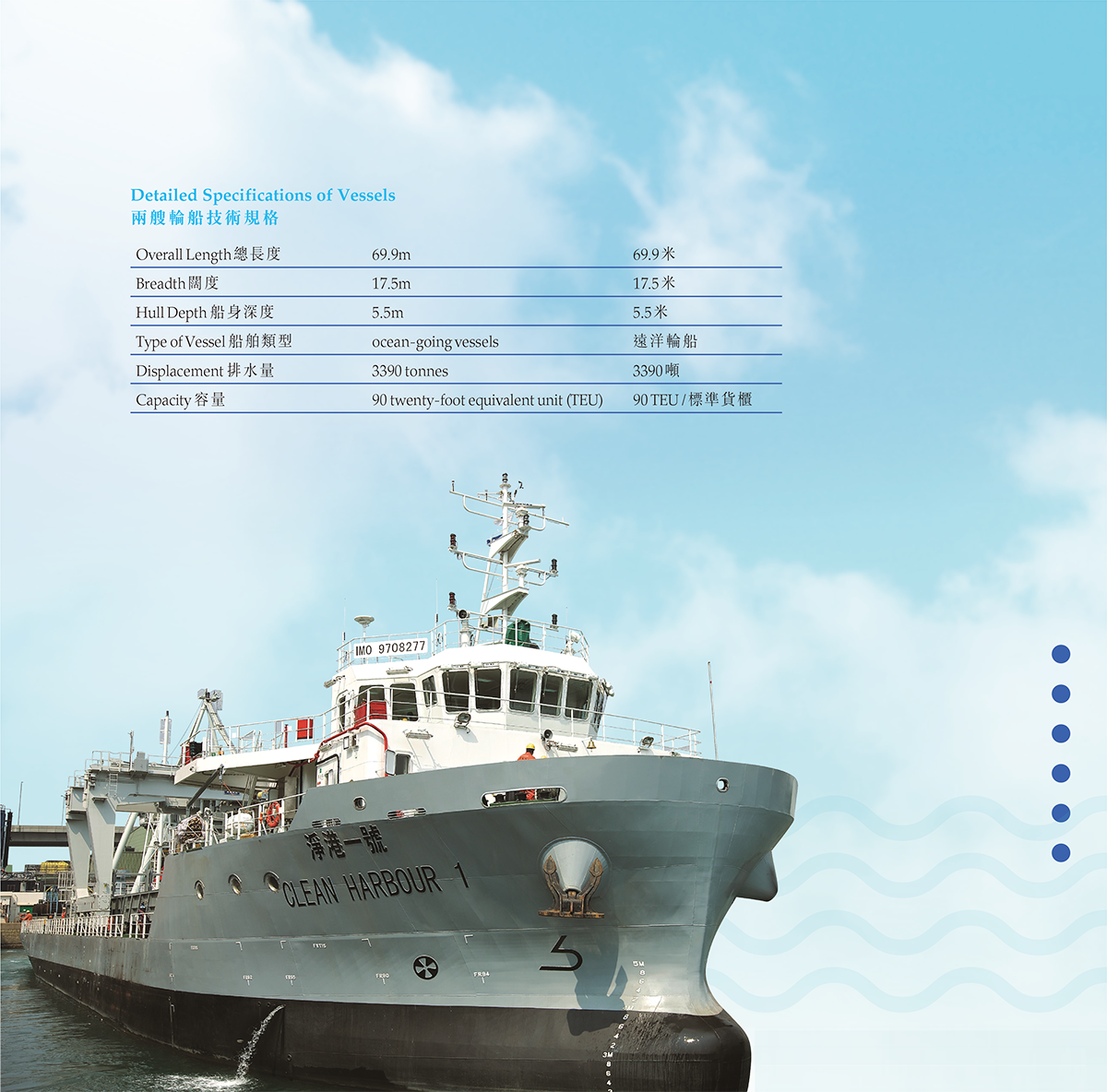
Environmental Features
The two vessels are the first-ever diesel-electric cargo vessels to be registered in Hong Kong. To reduce their carbon footprint, they are propelled by electric motors using power generated from ultra-low-sulphur diesel or biodiesel. Compared to conventional diesel drives, diesel-electric propulsion systems are technically and operationally superior, with optimal manoeuvring and positioning properties, low vibration and noise levels, and improved fuel efficiency.
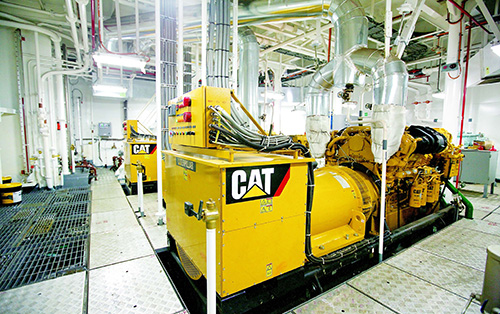
Biodiesel power generator
When berthed, the vessels are connected to an on-shore power supply, eliminating the use of diesel to further reduce emissions. Compared with ordinary diesel vessels, Clean Harbour 1 and Clean Harbour 2 together can cut carbon dioxide emissions by up to 130,000 kg per year, which is equivalent to the annual carbon dioxide absorption capacity of 6,000 trees.
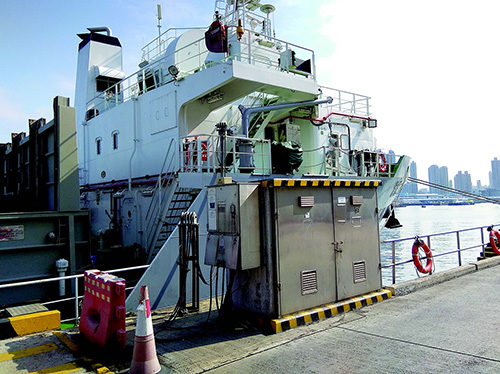
Connected to on-shore power supply when berthed
Vessel Design
The new vessels feature a double hull design such that the inner hull will remain watertight in case of damage to the outer hull, allowing the vessel to return safely to the dockyard for repairs. The navigation system includes onboard radar, an electronic chart system, magnetic and gyro compass systems, a depth sounding system, a bridge sound reception system to enable crew to hear fog horns and receive other signals, and other equipment.
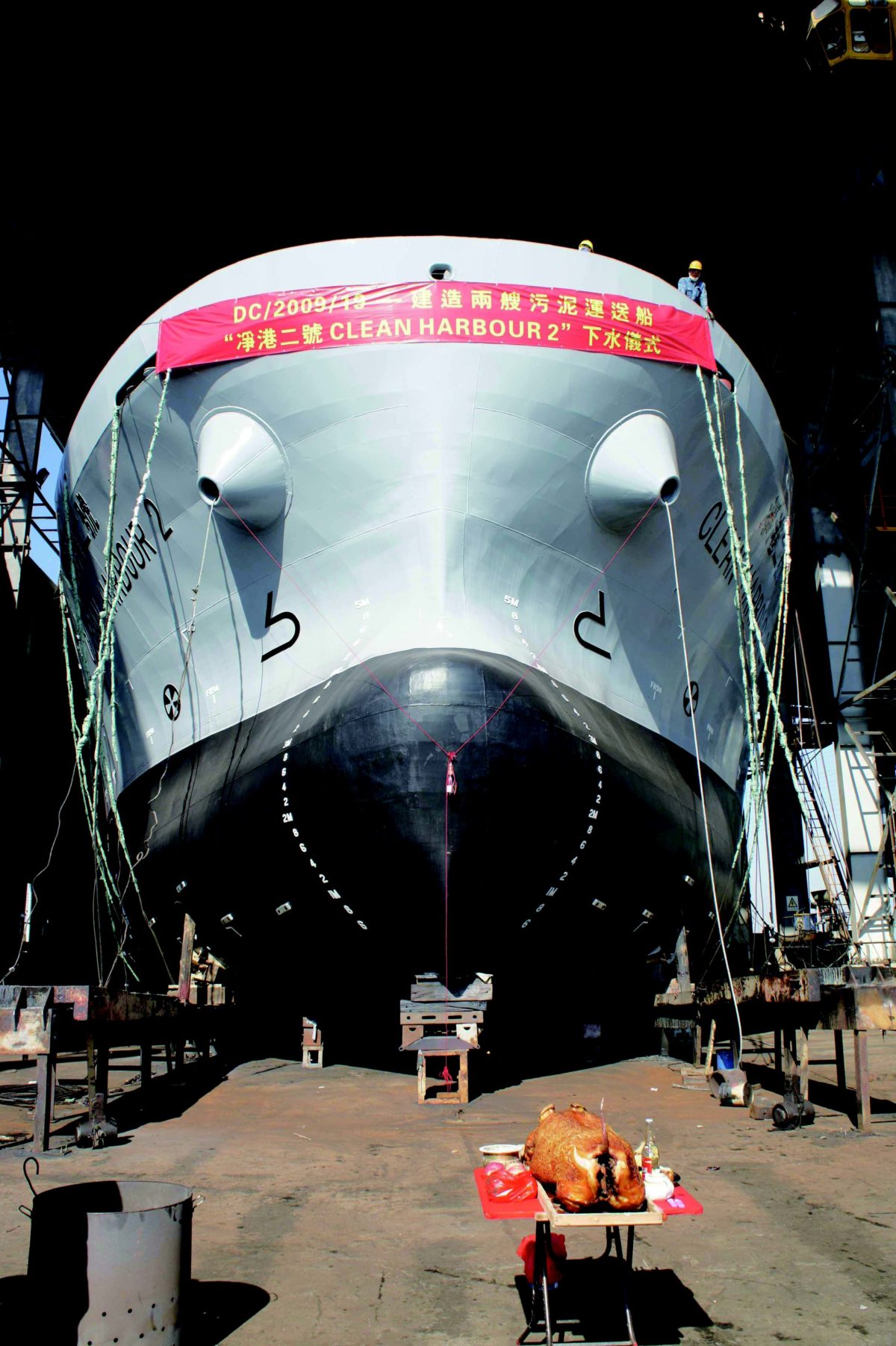
Clean Harbour 2 launching ceremony
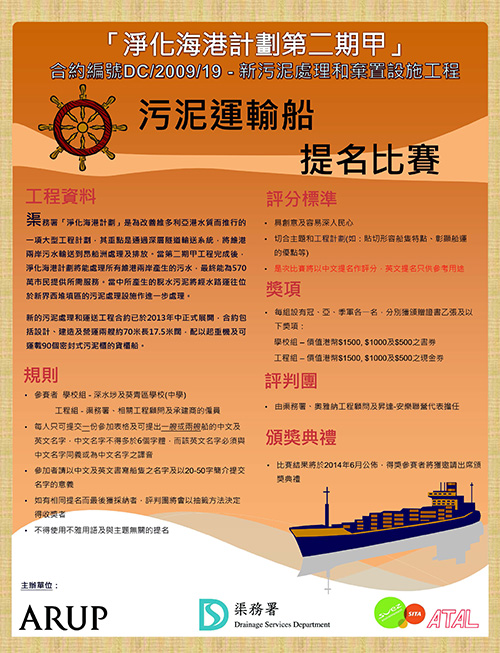
Vessel naming competition
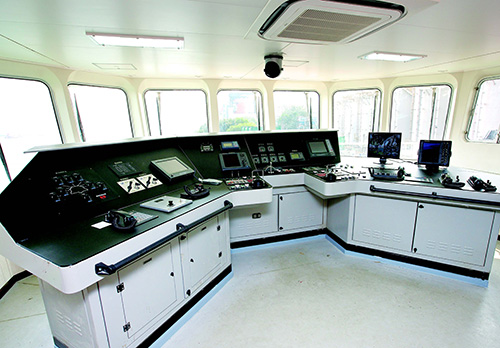
Control panel
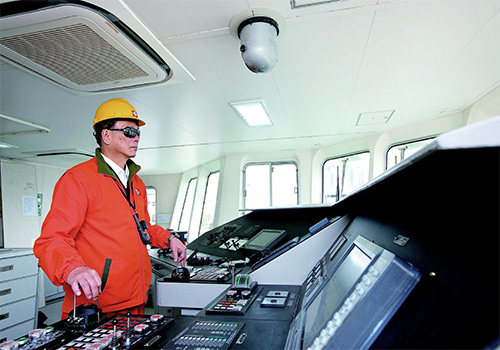
Captain in wheelhouse
The vessels are also equipped with an overhead gantry crane for the direct loading and unloading of sludge containers from lorries. The crane can handle 20 containers in one hour. The gantry crane also minimises the chance of damage to the containers during loading and unloading even in rough sea conditions.
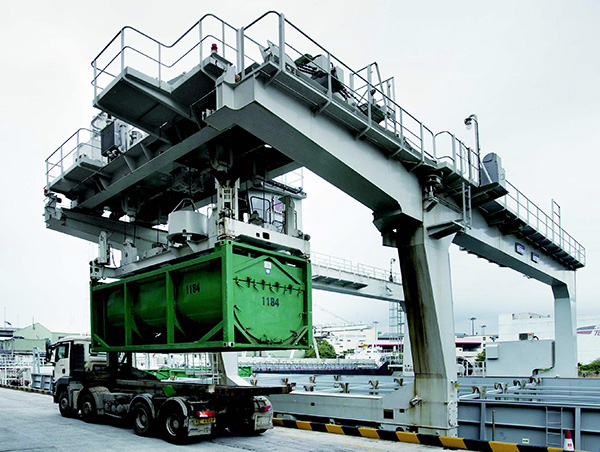
Overhead gantry crane
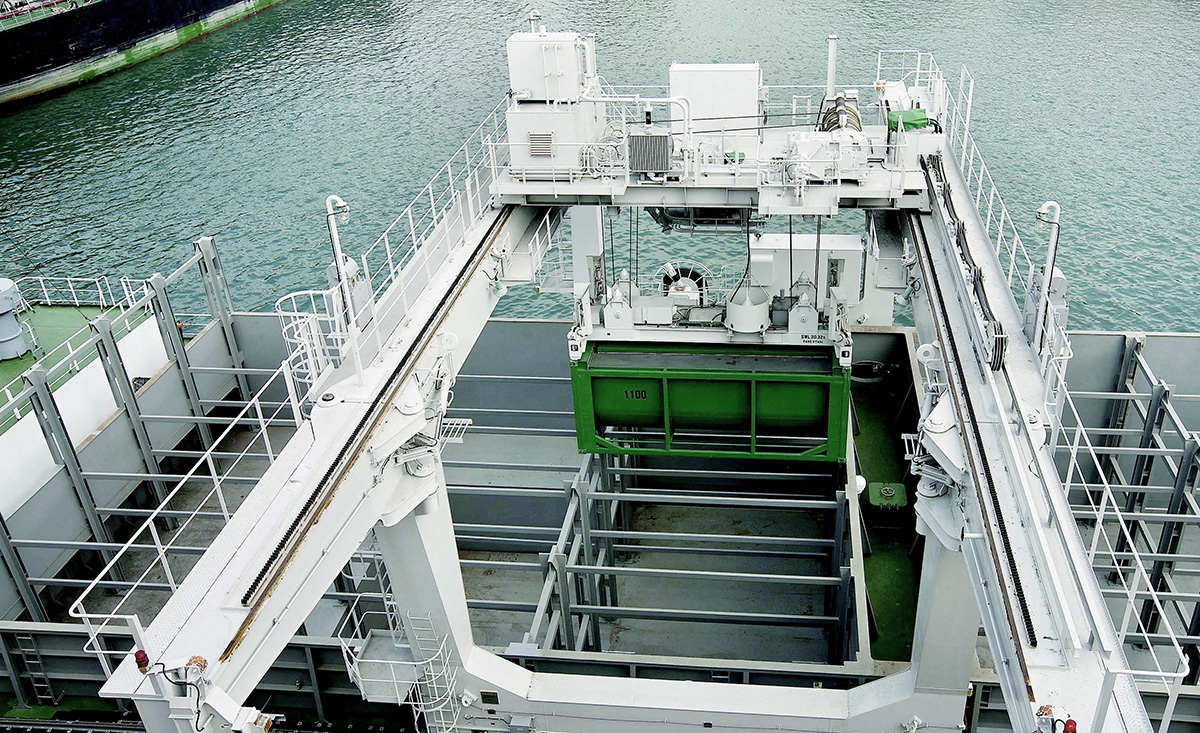
Loading and unloading of sludge containers
Let the Sailing Begin!
After undergoing thorough stability tests and a number of sea trials, Clean Harbour 1 and Clean Harbour 2 set sail on 5 March 2015, loaded with sludge to fuel T · PARK operations. A new journey had literally begun for HATS — a journey of waste-to-energy transformation that has seen our two new vessels move HATS sludge from Stonecutters Island to Tuen Mun day after day ever since.
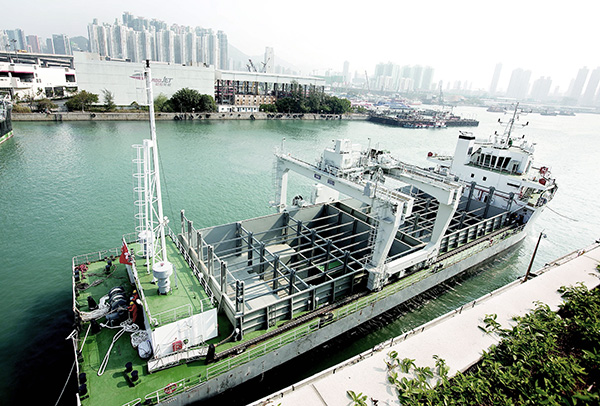
Clean Harbour 1 set sail
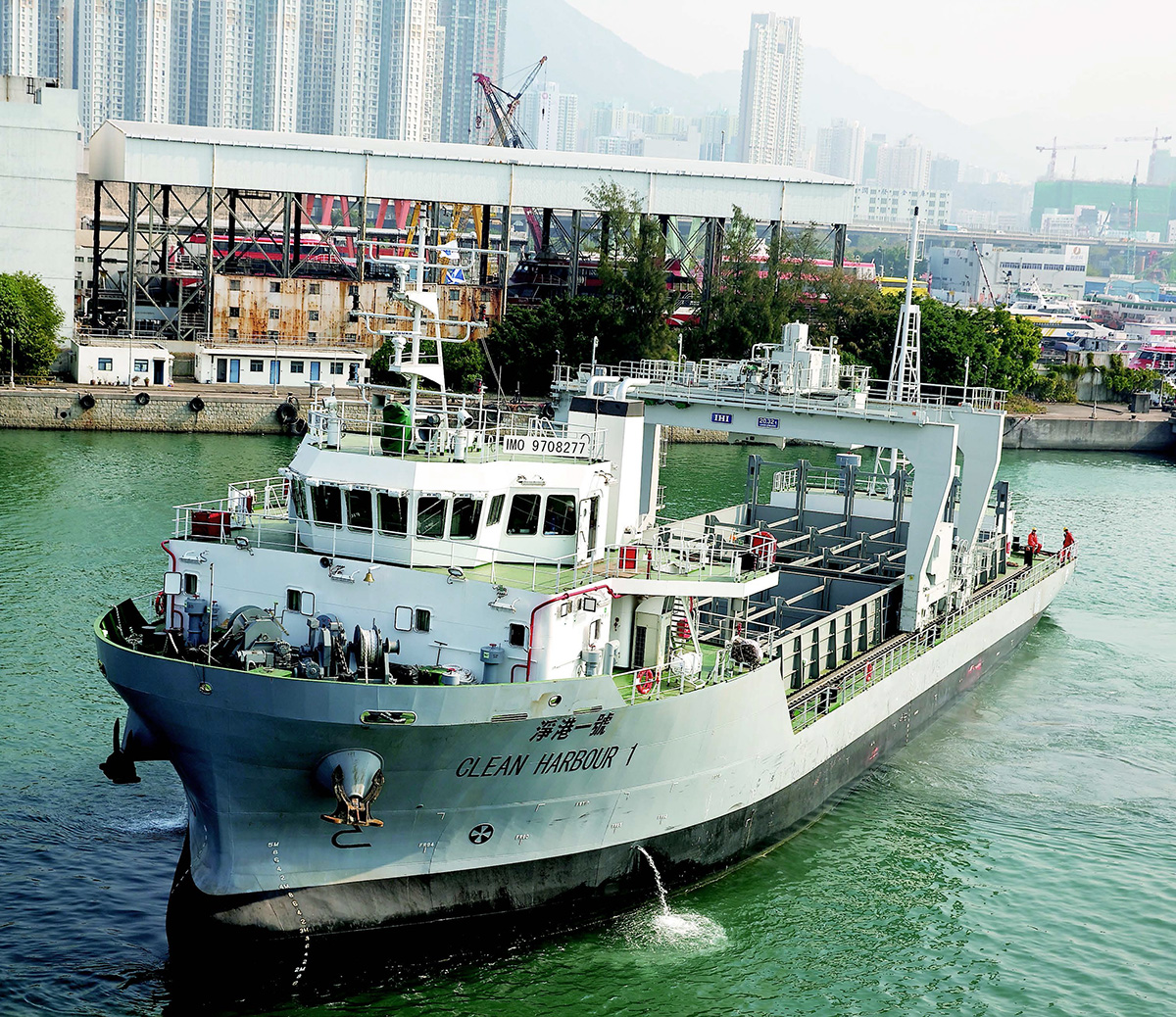
POSTSCRIPT
“I am privileged to have had the opportunity to participate in the HATS project which spanned over20 years. Numerous difficulties and setbacks were encountered, particularly during Stage 1. Westrived to overcome the engineering challenges and conducted extensive public consultations. All difficulties were eventually resolved satisfactorily.”
“HATS often gave us interesting assignments never imagined before, such as designing two ocean going vessels. The vessels were built to transport sludge to T · PARK for incineration and electricity generation to complete the waste-to-energy loop. The process of designing sea vessels was very satisfying indeed!”
Henry CHAU Kwok-ming
System Advisor,
Drainage Services Department

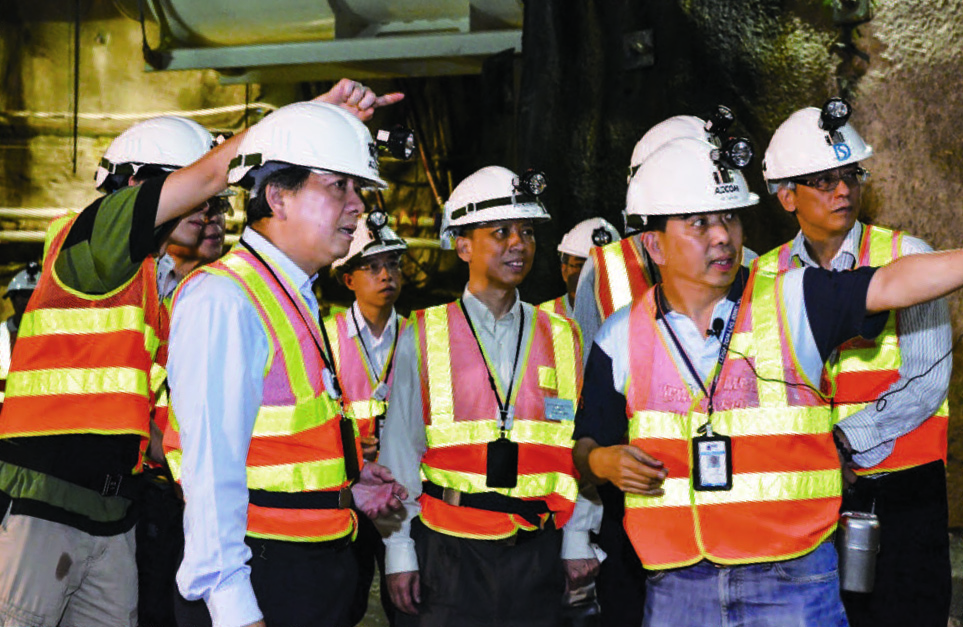
